Kuebler incremental encoder application guide
Wednesday, 17 November, 2021 : 13:29 Tips and help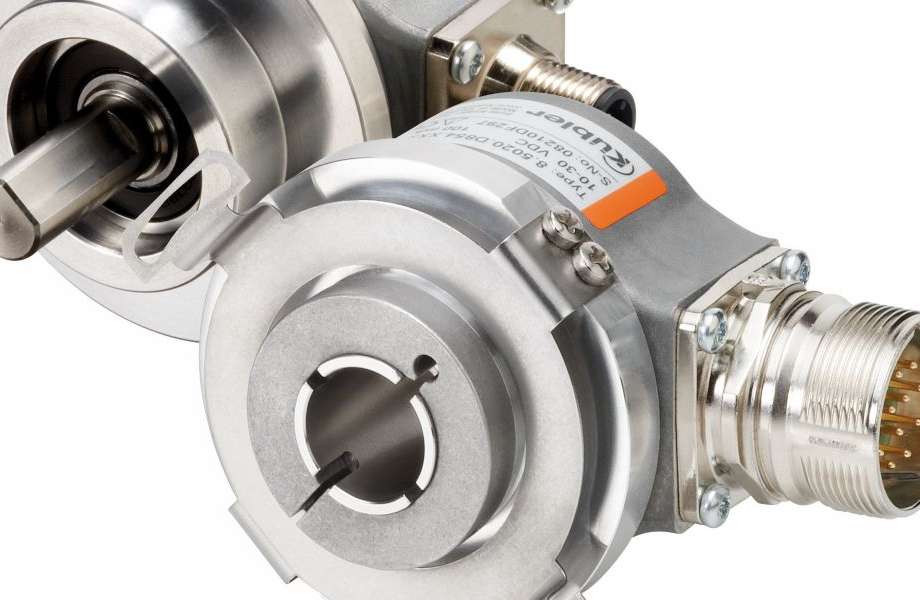
2Description
When you have to select an encoder for a motion control application, you are confronted with numerous technical terms. The amount of data available can be overwhelming. Which critical terms should you focus on first, and which ones can be deferred?This document deals with three important concepts that deserve your attention: Resolution, accuracy and precision.
3Resolution
In mathematics, natural sciences and engineering, the resolution describes the smallest division that can be measured or observed.3.1Incremental encoder resolution
The resolution of incremental encoders is the number of pulses (high / low change) which are emitted within one revolution.The required angular or linear resolution of an application determines the number of pulses per revolution. Linear movements must first be converted into rotary movements (e.g. by a measuring wheel).
The encoder resolution is given in pulses per revolution [ppr] The mechanical resolution
As a rule, the mechanical pulse number of a rotary encoder cannot be changed subsequently.
Electrical resolution
The resolution gives us the smallest distance that can be measured.
If you divide a complete rotation, 360° mechanically, with the number of impulses you get over the rotation, you get the angle per impulse.
Example:
Given:
- Resolution of the encoder = 3600 ppr Wanted:
- Angle per pulse
𝐴𝑛𝑔𝑙𝑒 𝑝𝑒𝑟 𝑝𝑢𝑙𝑠𝑒 =
360°

𝑅𝑒𝑠𝑜𝑙𝑢𝑡𝑖𝑜𝑛 [𝑝𝑝𝑟]
𝐴𝑛𝑔𝑙𝑒 𝑝𝑒𝑟 𝑝𝑢𝑙𝑠𝑒 =
360°

3600 𝑝𝑝𝑟
The encoder moves at an angle of 0,1° per pulse
- Incremental linear resolution
For a linear measurement with a rotary encoder, the linear movement must be converted into a rotary movement. This can be converted by a measuring wheel or a wire draw. An encoder is equipped with a measuring wheel. Per revolution there is a distance of 200 mm (circumference).

- circumference of the measuring wheel = 200 mm
- Measuring resolution = 0.1 mm Wanted:
- Resolution of the encoder [ppr]
𝑅𝑒𝑠𝑜𝑙𝑢𝑡𝑖𝑜𝑛 =
𝐶ircumference

𝑀𝑒𝑎𝑠𝑢𝑟𝑖𝑛𝑔 𝑟𝑒𝑠𝑜𝑙𝑢𝑡𝑖𝑜𝑛
𝑅𝑒𝑠𝑜𝑙𝑢𝑡𝑖𝑜𝑛 =
200 𝑚𝑚

0,1 𝑚𝑚
To achieve a measuring resolution of 0.1 mm, a 2000 ppr encoder is required.
3.3Scanning incremental optical
The signals are generated using the transmitted light method, comparable to an optoelectronic fork light barrier.
![]() |
![]() |
||
A sectional view of a rotary encoder model.
The LED with convergent lens, a diaphragm, the code disc and the sensor array on the printed circuit board can be seen here.
When the encoder shaft rotates, the code disk moves over the code mask. The sensor array is alternately illuminated with light/dark.
![]() |
This results in a sinusoidal voltage output at the sensor array. This in turn is converted into a square wave signal via a Schmitt trigger. A light/dark change corresponds to one pulse. Incremental encoders typically have between 1 and 5000 pulses.
3.4Scanning incremental magnetic
![]() |
Unlike optical encoders, the magnetic system consists of two components:
- The sensor head with integrated electronics
- The pole wheel
The pole wheel consists of a hub on which a ferromagnetic layer is applied. This is alternately magnetised with north and south poles. The pole pairs are usually 2 or 5 mm long. Therefore the number of pole pairs depends on the outer diameter of the pole wheel.

![]() |
|||
![]() |
|||
The resolution of magnetic sensors is calculated from the number of pole pairs multiplate by the interpolation factor.
3.5Incremental signals and multiple evaluation
Single-channel encoders:
Single-channel encoders are used wherever direction detection is not necessary, e.g. speed and length measurement.Two-channel encoders:
Applications in which the direction of rotation is to be detected, e.g. positioning, require encoders with two channels A and B electrically shifted by 90° against each other. The direction of rotation is determined by evaluating the phase relationship.Channel A precedes channel B, if the encoder shaft rotates clockwise, looking at the shaft / with hollow shaft encoder looking at the flange.
Three-channel encoders:
In addition to the two channels A and B there is a zero pulse, which occurs once per revolution and can usually be used for the reference run (zeroing) of a machine. The 0-pulse is gated with channels A and BAgain, channel A leads channel B when the encoder shaft rotates clockwise, looking at the shaft / with hollow shaft encoders looking at the flange.

Inverted signals
In environments where interference on the signal lines is to be expected, or in the case of very long supply lines, we recommend the use of encoders with additionally inverted signals (complementary signals).
![]() ![]() ![]() ![]() |
With pulse multiplication or multiple evaluation, the channels and edges are evaluated differently. The resolution of a two-channel encoder can thus be doubled or quadrupled by evaluation in the subsequent electronics.
In the simple evaluation, only the rising edges of channel A are counted, each rising edge is a counting pulse, channel B is only used to indicate the direction. If channel A leads channel B, the direction of rotation is cw (clockwise), if channel B leads, the direction of rotation is ccw (counter clockwise).
![]() |
With the double evaluation the rising and falling edges of channel A are counted, each rising and each falling edge results in a counting pulse, channel B is only used to indicate the direction. If channel A leads channel B, the
direction of rotation is cw, if channel B leads, it is ccw.

With quadruple evaluation, the rising and falling edges of channel A AND channel B are counted, each rising and each falling edge of channel A and channel B results in a counting pulse, whereby the phase position from A to B again only serves to indicate the direction. If channel A leads channel B, the direction of rotation is cw, if channel B leads channel A, the direction of rotation is ccw.
Thus, a rotary encoder with 5000 physically existing pulses can generate 10,000 or 20,000 pulses per revolution, depending on the evaluation.

With quadruple evaluation, the rising and falling edges of channel A AND channel B are counted, each rising and each falling edge of channel A and channel B results in a counting pulse, whereby the phase position from A to B again only serves to indicate the direction. If channel A leads channel B, the direction of rotation is cw, if channel B leads channel A, the direction of rotation is ccw.
![]() |
Thus, a rotary encoder with 5000 physically existing pulses can generate 10,000 or 20,000 pulses per revolution, depending on the evaluation.
3.6Output frequency Incremental encoder (pulse frequency)
The pulse frequency of the encoder must be considered from two points of view.- What is the maximum allowed output frequency of my encoder?
- What is the input frequency of the pulse inputs of the controller or encoder card?
Example:
Given:
𝑃𝑢𝑙𝑠𝑒 𝑓𝑟𝑒𝑞𝑢𝑒𝑛𝑐𝑦 =
60
𝑃𝑢𝑙𝑠𝑒 𝑓𝑟𝑒𝑞𝑢𝑒𝑛𝑐𝑦 =
3000−1 𝑥 1000 𝑝𝑝𝑟

60
Given:
- Speed = 3000−1
- Resolution of the encoder = 1000 ppr Wanted:
- Pulse frequency of the encoder

60
𝑃𝑢𝑙𝑠𝑒 𝑓𝑟𝑒𝑞𝑢𝑒𝑛𝑐𝑦 =
3000−1 𝑥 1000 𝑝𝑝𝑟

60
This results in a pulse frequency of 50 kHz.
The pulse input of the controller or the encoder card must be able to process this frequency.
3.7How high must the resolution be in the application?
All incremental encoders are generally available with different resolutions. At Kübler the resolutions for standard encoders are between 1 ... 5000 pulses per revolution and for high resolution encoders up to 36000 pulses per revolution.Is it "best practice" to always choose the highest possible resolution? Of course not. It rather depends on the application and the marginal parameters. For example, at a very high speed it might be better to choose a lower number of pulses, otherwise the output frequency might be too high or the input frequency of the evaluation too low. With very slow movements it is usually more sensible to select a high resolution and to be able to detect the smallest possible movements.
4Accuracy
The accuracy in general, describes the agreement of the target measured value with the actual measured value
![]() |
The accuracy of an encoder is given in electrical degrees or as part of the grating period.
The accuracy of the output signal sequence of an encoder depends mainly on the following conditions:
- Error in the grid division of the code disc.
- Error in the grid division of the code mask.
- Eccentricity of the code disk to the shaft.
- Runout deviation of the bearing.
Measuring the accuracy of an encoder is a complex process that requires sophisticated and well calibrated equipment, in which the encoder shaft is moved through 360° and the output values are permanently compared to a highly accurate reference system. In addition, measuring the accuracy is a very time-consuming process. Therefore, at Kübler the accuracy of the encoders is not measured permanently and for each individual piece, this would only drive up costs and thus prices.
The accuracy specifications are given in angular minutes or angular seconds. In addition, a typical accuracy value and a minimum accuracy value are given.
e.g. Sendix 5000 encoder with 2048 pulses: Typically 45 angular seconds = 0.0125°.
Minimum 75 angular seconds (or 1 angular minute 15 angular seconds) = 0.02083°.
These values apply to an unloaded shaft and encoder temperature between 20° and 40°C.
In general, you must keep in mind that an encoder is always only a part of a complete system and therefore other factors must also be considered when determining the system accuracy of a system/application. These include among others
What happens if we make a second rotation and measure the accuracy again? Do we get the same error at every position? What happens after a third, fourth or fifth rotation?
Is the position error repeatable or does it vary?
The repeatability or precision of an encoder is a measure of the reproducibility of a measured value under constant measuring conditions. Or also the maximum deviation of a measurement which repeatedly reaches the exact same measuring point.
Let's compare this with the results of two archers, which one is more accurate and which one is more precise?
Surprisingly, the average accuracy is similar for both targets. The average position of all arrows on the left side is in the middle of the target, just like the arrows on the right side, all arrows are on the same ring. The difference between the two is the precision of the shots. The hits on the right side are accurate but not precise. The hits on the left side are both accurate and precise.
- Motor
- Motor shaft
- Encoder Coupling
- Encoder mounting
- Environmental influences such as temperature
- …
5Repeatability or also precision
As we have seen in the Accuracy section, to determine the accuracy of an encoder we can rotate one 360° and measure and compare the accuracy.What happens if we make a second rotation and measure the accuracy again? Do we get the same error at every position? What happens after a third, fourth or fifth rotation?
Is the position error repeatable or does it vary?
The repeatability or precision of an encoder is a measure of the reproducibility of a measured value under constant measuring conditions. Or also the maximum deviation of a measurement which repeatedly reaches the exact same measuring point.
Let's compare this with the results of two archers, which one is more accurate and which one is more precise?
![]() |
![]() |
Surprisingly, the average accuracy is similar for both targets. The average position of all arrows on the left side is in the middle of the target, just like the arrows on the right side, all arrows are on the same ring. The difference between the two is the precision of the shots. The hits on the right side are accurate but not precise. The hits on the left side are both accurate and precise.
6Summary
We have got to know three important terms for encoders.Resolution - is the number of pulses per revolution of an encoder
Accuracy - the difference between target and actual position
Precision - the difference between repeated measurements under identical conditions
Although the three terms may appear to be identical or similar, in reality they are completely independent of each other. Understanding resolution, accuracy and precision will help you make decisions when choosing an encoder.
Here again the comparison of resolution, accuracy and precision
![]() |
![]() |
![]() |
![]() |
|
|
|
|
Practical advice on sample applications, when I need which resolution or accuracy.
- High resolution without high accuracy e.g. for speed control at very low speed.
- High resolution with high accuracy e.g. CNC axis